Tips for Optimizing Flex PCB Design
For combining the best of both worlds—the standard rigid printed circuits with flexible circuits on a single board—Rush Flex PCB offers their rigid-flex PCB design. Typically, these boards primarily consist of flexible polyimide strips connecting two or more rigid areas with copper cladding substrates. Through-holes on the rigid areas of the board connect their circuit to those on the flexible polyimide board.
The complexity of the rigid-flex boards requires a lot of attention while designing them. By using our design methodologies and tips it is possible to fabricate not only highly reliable rigid-flex boards, but which are also capable of withstanding several hundreds of flex cycles without failure.
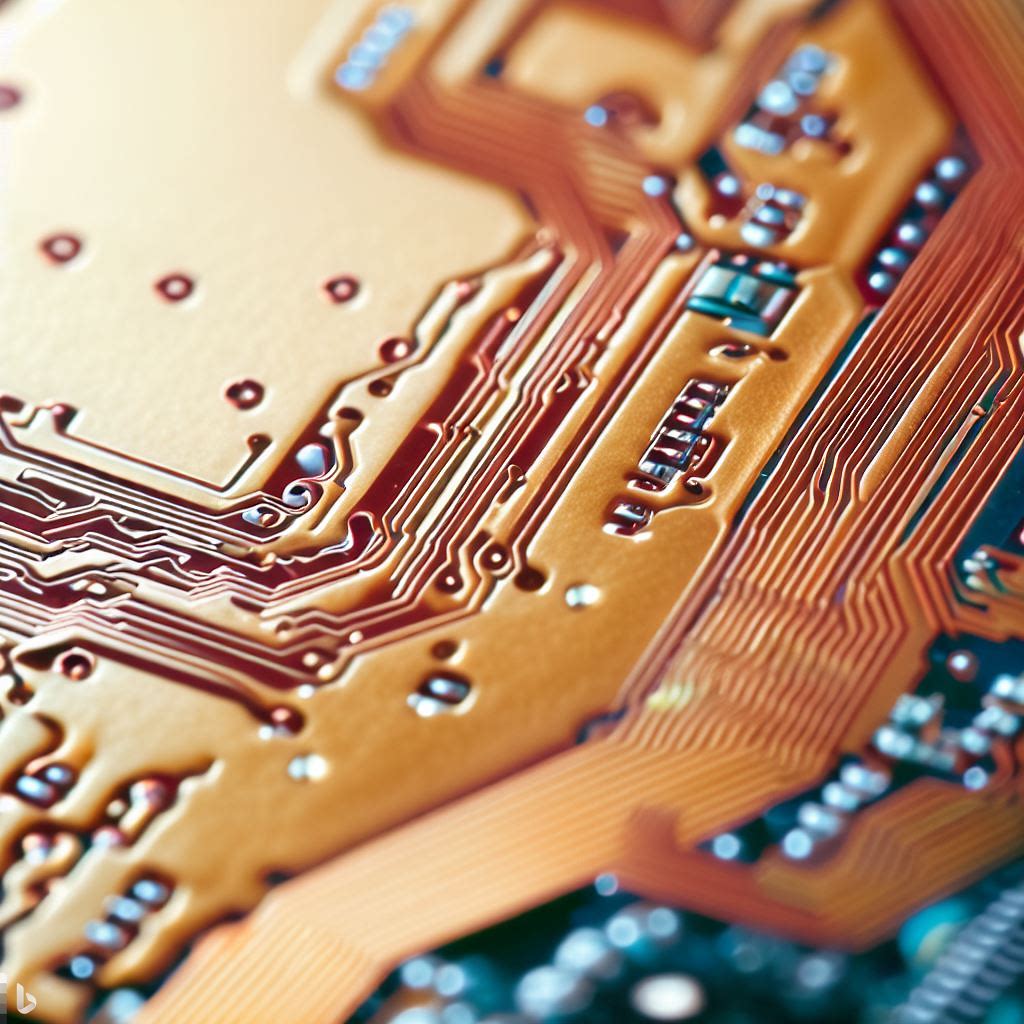
Reasons for Flex PCB Use
When it is necessary to interconnect multiple subcircuits, one of the alternatives is the use of connectors, especially for effective transport of power and signal through individual subcircuits. However, connectors add cost and also provide additional opportunities for failure. Moreover, connectors being physically large, require more space in the system.
This is where the rigid-flex circuit technology comes in. Rigid-flex boards use built-in interconnects in the form of flexible circuits. There are several advantages to this design:
Physically smaller size — Absence of connectors makes the entire circuit light and small, taking up substantially smaller space.
Higher reliability — Without connectors, it is much easier to assemble rigid-flex circuits, as flexible circuits already interconnect the different subcircuits right after the manufacturing of the board. In high-vibration environments, where connectors are more likely to fail, the rigid-flex circuit structure is more reliable, as it can absorb vibrations in a better way.
Space-Saving — As the flex circuit can bend and fold into a smaller profile, it offers significant space-saving opportunities for using a small enclosure.
The rigid-flex PCB design has some disadvantages also that designers need to look into while verifying whether this design-type really suits the application. As the production process of rigid-flex circuits is significantly more complex compared to regular rigid boards, the production yields are likely to be lower. Fabrication costs for rigid-flex boards are also higher on account of the manufacturing cycle being longer.
Basics of Rigid-Flex PCB Design
Once the designer has decided the suitability of rigid-flex circuit for their application, they must consider:
- The intended environment for the board
- Whether the board is meant for a dynamic bend or a stable bend
- The bend radius
- Placement of vias and traces
- Design of power and ground planes
Operating Environment
It is necessary to know the intended environment in which the board will operate. The rigid-flex design typically operates within an enclosure. The designer must consider the mechanical stresses and forces that may affect the board. They must ensure the design of the board within the enclosure must be capable of dealing with those forces and stresses.
Type of Bend
If the board is meant for a stable bend, the operator will bend it while installation, and it is meant retain this shape without change. Designers make sure the bend radius is about ten times the thickness of the flexible substrate.
However, when the board is meant for a dynamic bend, it will be constantly subjected to bending and unbending stresses throughout its working life. Designers typically use only one or two layers for flex boards meant for dynamic bending operations. They ensure that the bending radius is at least a hundred times that of the thickness of the flexible material.
Placement of Holes and Vias
The area of the flexible circuit that undergoes bending is its most delicate part. Designers typically avoid placing holes, pads, and vias in the bend areas. Areas close to the bending lines can stress the structure of a plated hole close to it. Designers prefer to keep all pads and vias in areas that are not subject to bending, that is, on the rigid, hard section of the board.
However, sometimes it is inevitable that holes and vias appear on the flexible section. In such situations, designers prefer to use anchors for strengthening them, while adding teardrops to connect them to traces. In such cases, the rule of thumb is to use 10 mil holes with at least a 10 mil annular ring around them. The larger size anchors the pads, thereby preventing any peeling during the flexing. Designers typically place holes and vias at least 15 mil away from the edge of the stackup.
Placement of Traces
In regard to traces and routing, designers prefer to position the traces as perpendicular, straight lines. For boards that bend or fold along a horizontal line, designers prefer to place the traces vertically. Ideally, all traces should go in one direction, but in case a change of direction is necessary, designers prefer to curve the traces rather than use sharp corners of 45 or 90 degrees. They do this to eliminate high-stresses on the trances. Another way designers decrease areas of high stress is by using narrow traces spread out across the flexible area.
It is a standard practice to add in dummy traces and redundant traces to increase the mechanical sturdiness of the flexible areas. For boards subject to dynamic bending, adding dummy/redundant traces prevents traces from breaking the signal path totally.
In case a flex circuit has traces on both, the top as well as the bottom sides of the flexible section, it is customary for the designer to alternate them such that no bottom-layer trace has any top-layer trace immediately above it, and no top layer trace has a bottom-layer trace immediately below it.
Design of Power and Ground Planes
In conventional PCB design, it is customary to use a continuous solid area of copper pour for power and ground planes. However, doing the same for flex PCB design will add a significantly large amount of stress on the board, while reducing its flexibility. Rather than use solid areas of copper, for flex circuits, designers prefer to use hatched-polygon patterns for planes. To gain maximum flexibility, they minimize the trace widths on the fill. However, cross-hatch patterns are not suitable for high-speed signal integrity.
High-Speed Design
Because if layer stackup, impedance control can be somewhat of a challenge on rigid-flex PCB designs. Designers typically use a co-planar stripline construction on single-layer flex circuits, where the signal layer alternates with ground strips. However, this is susceptible to EMI.
Better results are possible with two layer flex stackups. Here, designers can use a microstrip structure that is suitable for 50 ohm circuits. Although higher layer counts offer the ability to create a standard construction like stripline, the extra layers will tend to reduce the flexibility of the circuit.
Design Standards for Rigid-Flex PCBs
Among the numerous standards available for rigid-flex board design, IPC 2223 specifies the coverlay construction, air gaps, adhesive flex cores, strain relief filets, and the pre-bake requirements. It also has numerous tips for locating plated vias or holes near the transition zone where the rigid part changes over to the flexible part.
The transition zone is especially unique, as the polyimide coverlay encapsulating the flexible area overlaps the rigid areas by a small distance. During the lamination process, this ensures the rigid area encapsulates the flexible area through the adhesive. The coverlays attach to the flex surface using acrylic or epoxy adhesives. If vias are present in this area, the expansion, or contraction of the adhesive may subject them to stress, as the adhesives typically have a high thermal coefficient of expansion during reflow.
Board Design and Stackup
For proper flex behavior, it is necessary for the designer to communicate with board manufacturers for deciding on usage of materials. This is necessary as several factors can affect the board’s ability to bend. Among these are:
- Mask types
- Dielectrics
- Stiffeners
- Thickness of copper layers
In addition, it is necessary to pay attention to other factors also. These are:
- Flammability rating
- Mechanical requirements
- Impedance control
While deciding the stackup design, it is customary to split it into three separate zones:
- Primary stackup or Zone 1 — for the rigid area of the board
- Zone 2 — for the flexible area of the board
- Zone 3 — also for the flexible area, but with stiffener applied, thus limiting its bending ability
In general, designers tend to sandwich the flex layer in between the rigid board. This reduces the stress on the system, as against placing the polyimide board in the top or the bottom layer, which can result in greater stress and adhesive peel off.
The outline of the board should not have sharp corners, as this can result in tearing. Designers typically use the filet tool in their PCB design software to round off any sharp corners.
Image Files for Flex Circuits
While getting the design to the manufacturer, it is necessary to use image files just as in regular PCBs. However, the organization and content of these files can be more complex in the case of flex circuits. Designers prefer the use of more intelligent data formats such as IPC 2581, rather than traditional fab and assembly files.
Conclusion
Most 2½-D design tools are adequate for designing conventional rigid boards, and they are suitable for flex circuits as well. However, as flex circuits have a unique bending nature, Rush Flex PCB recommends use of tools that can operate in 3D for visual verification and automated checking. Moreover, it is also necessary to configure flex design tools to meet the unique requirements of the above guidelines with respect to flex specific features and functionality.