Expert Guide to Flex PCB Thickness
Designing Flex PCBs needs an alternative approach as compared to regular rigid boards. It is necessary to optimize their design for different use cases and the materials they use, to allow them to provide maximum savings in operational flexibility, space consumption, and manufacturing costs. Rush Flex PCB is a pioneer in manufacturing flex PCBs, and provides an expert guide to what decides the thickness of flex PCBs.
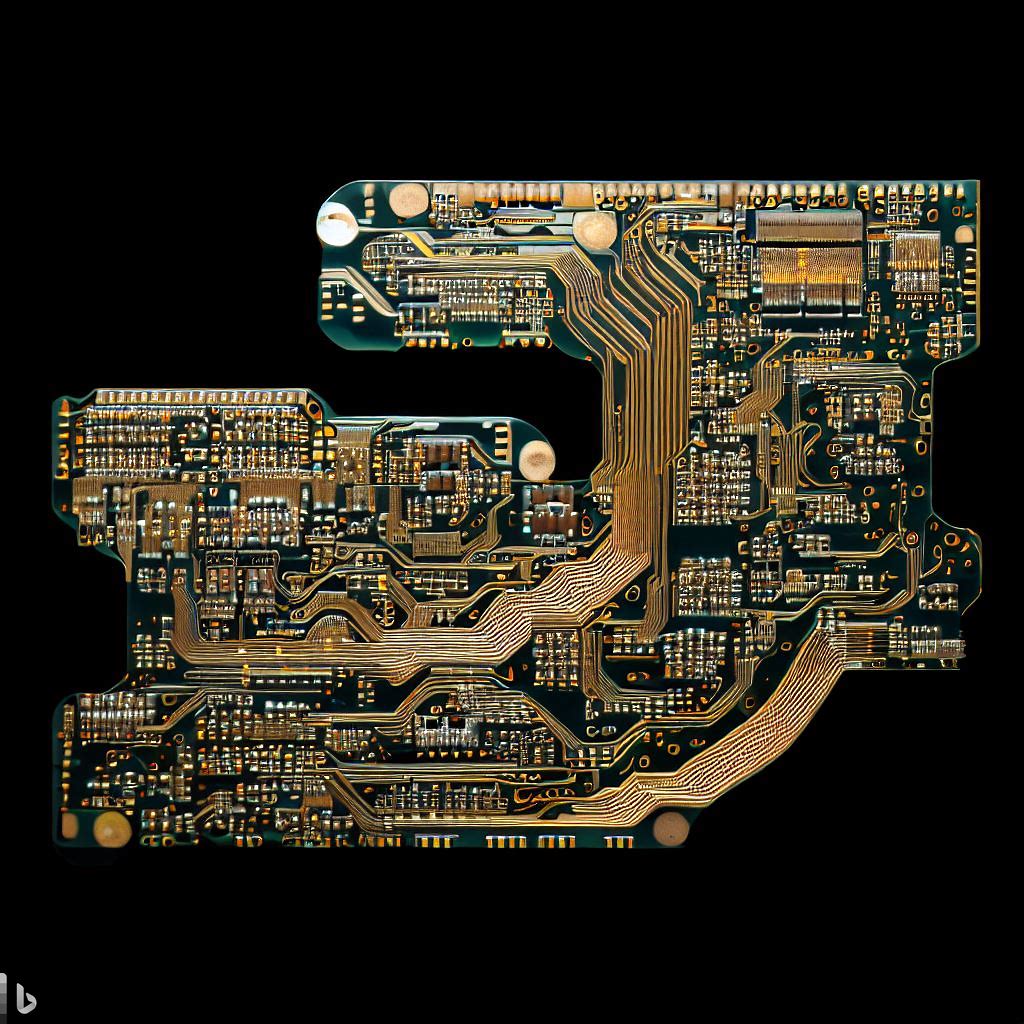
When designing flex PCBs, designers must consider many aspects. These include the board outline, its bending requirements, the stackup, placement of copper features, and most importantly, the material selection and the cost factor.
Any well-designed flex PCB will be easy to install. It will also be robust, reliable, durable, and lightweight. That makes flex PCBs eminently suitable for applications in various industries, including medical, IoT, wearables, automobiles, and aerospace. Flex boards are highly resistant to harsh environmental conditions and can endure vibrations and high temperatures much better than their regular counterparts can.
With a proper design, flex boards can be lightweight and reduce consumption of space significantly. They can also provide major savings in manufacturing costs. For that, the designer must optimize their design for the specific use case, along with selection of suitable materials. The designer must consider many factors, especially bendability, during the design.
What is Flex PCB Bendability?
One of the special features of flex PCBs is their flexibility, which enables installing them in restricted spaces. To make the PCB flex, the designer must understand bendability—the extent to which the board can flex without damage, and how many times it must flex in its lifetime.
For static flex PCBs, it is enough if the board flexes only about a hundred times in its lifetime. The design of static PCBs allows it to bend a few times during install at assembly. On the other hand, a dynamic flex PCB must flex regularly during its lifetime. Therefore, dynamic flex boards must be more robust, as they must bend tens of thousands of times.
To put it very simply, the thinner the board, the more easily it can flex. In other words, thicker boards will not bend easily. The stiffness of a flex board depends on many factors like:
- Material of the board
- Number of copper layers
- Thickness of the copper layers
- Adhesive thickness.
Two factors govern bendability. These are the bend radius, and the bend ratio. The bend radius defines the minimum radius through which the board can flex without damage to its internal or external layers. The designer must define this minimum radius early on in the design of the flex board. This will ensure that the board will have the necessary flexibility without causing damage to the copper circuits when executing the bend. The bend radius depends on the number of layers in the board, increasing with the number of layers. A smaller or tighter bend radius increases the probability of failure.
Bend ratio is a number based on the ratio of the bend radius to the board thickness. While static boards can do with a smaller bend ratio, dynamic boards require a bend ratio at least ten times more. For double layer boards, this number can be as high as 15, while bending is not recommended for multilayer flex boards.
Factors Affecting Flex PCB Bendability
Sharp bends at 90° can cause high strain on the layers of a flex board. During installation, it is recommended to use only gradual and large curves to prevent damage.
Plated through holes and components in the bend area. Being stiff parts, these affect bendability. It is recommended to avoid placing PTH and components in bend areas of a flex PCB.
Copper conductors running parallel to the bend axis can compromise the reliability of the board. It is recommended to place copper conductors only perpendicular to the bend axis.
If it is unavoidable to place copper conductors parallel to the bend axis, they must be reduced to smaller than 10 mils in width. Additionally, they must be placed within the neutral bend axis, to face the least compression or tension during bending.
Copper conductors can face high strain during bending if placed adjacent to each other in multi-layered flex boards. Designers should preferably stagger them to avoid the strain.
Factors Affecting PCB Flexibility
Several factors influence the flexibility of a flex board.
- The thickness of a flex circuit is the largest contributor to its flexibility. The thinner the board, the more it can flex.
- The thickness of the copper traces influences the flexibility. Thicker copper layers can reduce the flexibility significantly. Multilayer flex PCBs with high layer count are difficult to bend. One method designers use to reduce copper thickness is to use cross-hatching, especially on ground planes on either side of signal layers.
- If the board is designed for smaller or tighter bend radius, it will have high flexibility. However, this also increases the chances of damage during flexing. The designer must, therefore, exercise an optimum tradeoff between a small bend radius and the extent of bending of the board.
- Introduction of slots or cutouts can help minimize the bend radius, provided the flex circuit has no copper traces in the bend region. This also reduces the amount of material in the bend region. It is possible to improve flexibility substantially by judiciously removing sections of the flex where there is no circuitry.
Flex PCB Materials
Designers must be aware of and have adequate knowledge of materials they would like to use for their flex PCBs. They can find a prescription of different materials and their specifications in IPC standards 4202, 4203, and 4204. The choice of PCB materials and their characteristics depends on the application and the design criteria of the flex PCB. Several properties are important here, including:
- Resistance to fire
- Resistance to moisture absorption
- Glass Transition Temperature – Tg
- Dielectric Constant – Dk
- Coefficient of Thermal Expansion – CTE
Constituents of Flex PCBs
In comparison with regular rigid boards, designers choose materials for flex boards to achieve better material properties. There are several constituents of flex PCBs:
Copper-Clad Laminate
This is the core component in a flex board, comprising layers of copper foil and polyimide. Flex boards typically use rolled annealed copper, as it offers higher ductility, making it more suitable for dynamic applications, and allowing achievement of tighter bend radius.
There are two major types of copper-clad laminates in popular use—adhesive-based and adhesive-less. Typically, fabricators use adhesives to laminate the copper layer on the core (polyimide). However, using adhesives often causes cracks to appear in the copper layer within the hole wall of plated through holes. This is due to the acrylic adhesive becoming soft when heated. Therefore, it is necessary to incorporate teardrops and anchors in the design for adhesive-based materials. Moreover, adhesive-based materials absorb moisture from the environment. Therefore, it is not advisable to use adhesive-based copper clad laminates in systems that will be exposed to the outside environment.
The introduction of adhesive-less copper-clad laminates has helped to avoid the above problems of adhesive squeeze-out, cracks, and dimensional errors.
Conductors
Conductors in a flex board are always made of copper, as it has high electrical conductivity. Typically, the copper is very thin, 0.5 oz, making it suitable for both static and dynamic applications. Depending on their current carrying requirement, flex boards may also use copper weights of 1 and 2 oz.
Bondply
These are composites made of polyimide films coated on both sides with an acrylic adhesive. Mostly used for encapsulating heavy copper in multi-layered flex boards, fabricators use bondply between two adjacent conductive layers of copper-clad laminates.
Adhesives
Manufacturers use various types of adhesives while fabricating flex boards. These include PSA or pressure sensitive adhesives, epoxy adhesives, and acrylic adhesives. Among them, PSA are the most popular, being flexible and offering superior bond strength. Another advantage is they adhere to the surfaces of substrates directly. Other adhesives, like epoxy-based and acrylic are available as flexible tapes, and are mostly thermosetting types.
The flexible tapes become tacky on application of heat and pressure, allowing securing of components in their places. To finalize the bond, it is necessary to cure it by applying additional heat and pressure.
For flex boards meant for dynamic applications, acrylic adhesives are more suitable, as they stay malleable even after curing. On the other hand, epoxy adhesive is not suitable for dynamic applications, as it becomes hard after curing. Therefore, when the PCB is a combination of both rigid and flex regions, the manufacturer uses epoxy adhesives for the rigid regions, and acrylic adhesives for the flex regions.
Stiffeners
Adding localized rigid materials in specific areas can help stiffen flex boards, if the application so demands. This is applicable for all types of flex boards, whether single-, double-, or multi-layered. Stiffeners can add mechanical support necessary when mounting components, increasing the strength, rigidity, and thickness of the flex part. Stiffeners may be made of stainless steel or aluminum, and fabricators use either pressure-sensitive adhesives or thermally cured acrylic adhesives to attach them. Stiffeners typically offer strain relief, heat dissipation, and weight balancing. In addition, they increase the abrasion resistance of the flex board, while helping to reinforce solder joints.
Surface Finish
Manufacturers prevent copper oxidation while providing a solderable surface on the flex PCB by applying a surface finish. There are several types of surface finishes to choose from, depending on the application. Fabricators protect the non-solderable parts of the flex board by using a coverlay, a liquid photo-imaged polymer, a photo-imaged dry film, or a covercoat.
Importance of Flex PCB Thickness
The application defines the constituents of the flex board, and ultimately, its thickness. For instance, the number of layers of circuitry on the board determines its thickness, the choice of materials determines its toughness and its capabilities in withstanding environmental stresses like vibration and high temperature. Most electronic equipment use multiple PCBs, which makes the decision of PCB thickness a design consideration. Manufacturers offer flex boards in standard thicknesses, of which 1.6 mm is a popular choice.
Factors Affecting Flex PCB Thickness
Layer Count
One of the major factors governing the thickness is the number of layers in the flex PCB. Moreover, the thickness of each layer is material-dependent, and based on whether the PCB is meant for dynamic or static flexing. While it is for the designer to decide the thickness of each layer, it is understandable that thicker layers will reduce flexibility, while allowing higher packaging density on a single PCB.
Copper Weight
The copper weight on each layer also significantly affects the ultimate board thickness. Copper weight is typically measured in ounce per square foot, and typically this is 1 oz/ft2 for flex boards. This copper weight allows for nine metal layers to be present on a board. While it is possible to get more metal layers by using thinner or different material, increasing the layer count can increase the board stiffness.
The thickness of the copper layer influences the appearance, size, cost, and flexibility of the board. However, as copper is essential to the board’s functioning, its thickness is essential.
Trace Width
Trace width influences the overall size of a flex board. Wider traces add to the PCB area necessary for components and shielding. For applications requiring very few traces on the flex part, traces of lower width may be an option for reducing the overall thickness of the board. Although 10-mil trace widths are typical for general purpose applications, designers often use 5-mil taces.
Conclusion
The size of the board determines its thickness and flexibility. Although flexibility is necessary for an application, it costs money. Therefore, Rush Flex PCB recommends experimenting with prototype flex boards of different thicknesses to determine the one performing best for the specific application.