An Expert Guide to Flex PCB Connectors
For printed circuit board parts like FPC or flex PCB connectors, Rush Flex PCB recommends using those conforming to the prevailing high industry standards. This is because, these crucial parts are essential for electronic devices, such as mobile devices, to not function. Being at the forefront of the highly competitive flex PCB industry, or exacting standards for all flex PCB connector products confirm to IPC Class 2 or 3. This boosts our customers’ confidence in working with us. When selecting flex PCB connectors, we ensure:
- Compatibility for thickness
- Proper pin pitch to match the width and pitch of the flex PCB
- Proper selection for the type of connector to suit the PCB type
- Proper selection for insertion into via, mechanical crimp, or ZIF socket
- Provide proper surface treatment for matching with connected sections.
Here, we are offering a comprehensive guide for selection and use of flex PCB connectors in the industry.
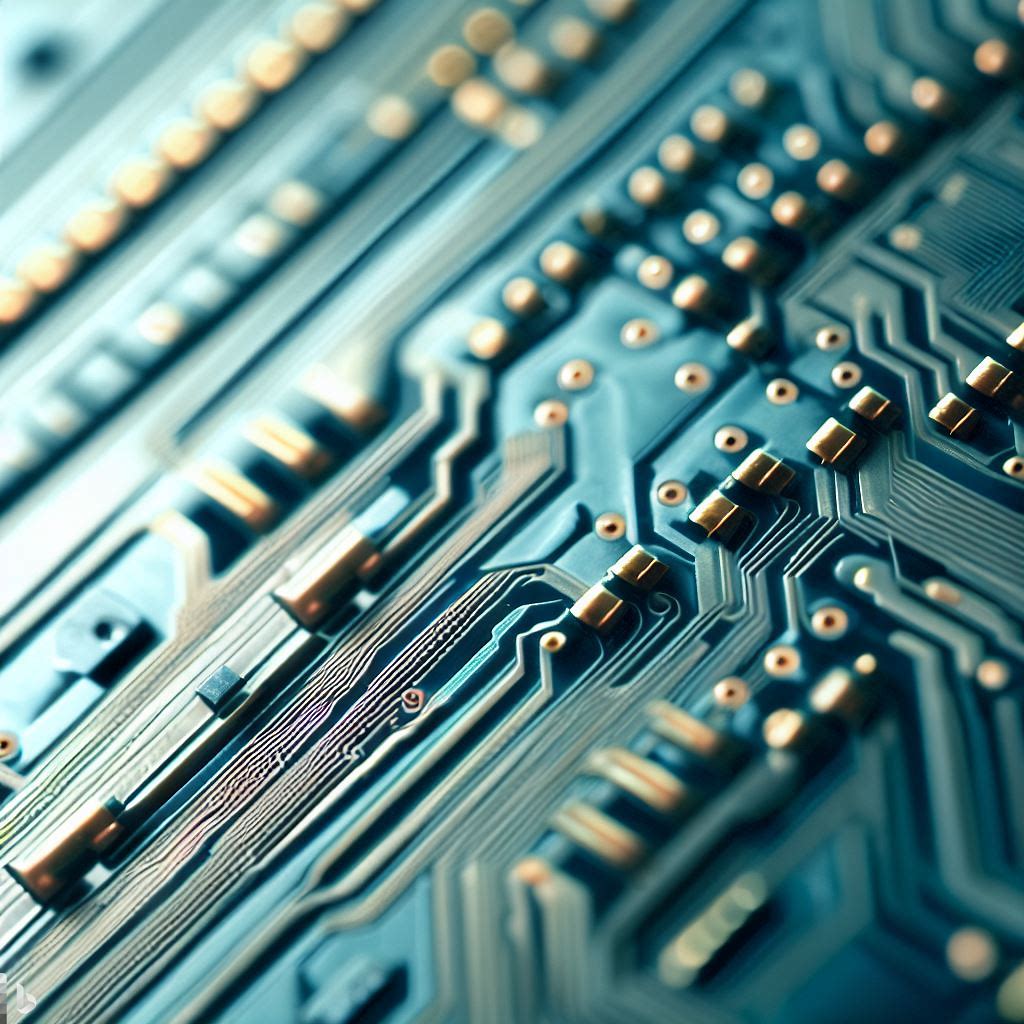
Expert Guide to Flex PCB Connectors
For transmitting or exchanging data and control signals, most PCBs need to connect to other PCBs or devices. Connectors facilitate these interconnections. The industry often uses flex PCBs to interconnect to rigid PCBs, thereby avoiding connectors. However, there are many interconnections that need the presence of a connector. Among these, flex PCB connectors are a subgroup of a larger group of PCB connectors that ease the interconnection process in the industry.
With electronic devices trending towards lower profiles, lighter connectivity, and smaller form factors, connector manufacturers have also taken up the challenge to make matching connectors, especially flex PCB connectors.
As a result, we have flex PCB connectors capable of fitting anywhere necessary in the system. Let us look at some types of flex PCB connectors available.
What Are Flex PCB Connectors
Flex PCBs use flex PCB connectors to provide complicated interconnections. Most flex PCB connectors are capable of handling clock intervals of about one second. They typically offer heights of less than one inch, while providing centerline and lightweight connections.
Catering to industry standards, flex PCB connectors focus primarily on compactness. In a majority of cases, installing FPCs require no tools. Users can choose from different pitches of these FPCs, starting from 0.25 mm, to 0.3 mm, 0.5 mm, 1.0 mm, and 1.25 mm.
It is easy to distinguish FPCs, as most have a low-profile design and miniscule dimensions. However, FPCs provide reliable interconnections, usually employing an actuator for clamping the cable terminations, thereby providing a secure connection.
Uses of Flex PCB Connectors
An FPC is not just another connector, but it is a PCB as well. Most FPCs are ultra-thin and lightweight. Although they primarily use flexible polymer film, they can be made from other flexible materials also. Their primary characteristic is flexibility, which makes them fit for innumerable applications.
In the electronic industry, FPCs are replacing not only typical rigid PCBs, but also conventional flex PCBs. Many applications today use FPCs to connect flexible PCBs with a flex PCB edge connector. This arrangement offers a suitable choice for requirements of lightweight features and enhanced flexibility.
For instance, the automobile industry is a very big user of FPCs. They use it in automobiles for providing lighting, autopilot facilities, navigation, entertainment, and for vehicular safety.
Another industry using FPCs in a big way is the wearables sector. Primarily in the medical equipment sector, applications include diagnostic equipment, hearing aids, internal organ monitoring, health monitoring, and many more.
The development of modern communication technologies has also increased the use of FPCs. Next generation electronics like 5G applications prefer using FPCs. The impressive range of flex PCB connectors make them eminently suitable for applications in sectors like automotive, automation, medical, commercial, and industrial.
Many other electronic devices use FPCs. Among them are cellphones, GPS tracking devices, hard drives, set-top boxes, desktop computers, Televisions, tablet devices, cameras, gaming consoles, Liquid crystal displays, and many more.
Being rugged and tough, FPCs can work undeterred in rough and challenging environments, along with extreme vibration and temperatures.
Special Flex PCB Connectors
An FFC or flexible flat cable is a connector that resembles a ribbon cable. The name flat cable is due to the wide and flat structure of the ribbon cable.
FFCs typically provide straight connections not needing any external parts. FFCs mostly use flexible plastic and polymer films for their construction. The end of the FFC typically has a metallic connector. The wire plane attatches to an integrated circuit, making the arrangement a flexible printed circuit board. FFCs are available in five pitch sizes of 0.5 mm, 1.0 mm, 1.25 mm, 2.49 mm, and 2.54 mm.
Their compact design gives the FFCs a relatively small footprint overall. Because of their thin and compact form factor, FFCs typically occupy less space compared to what traditional straight cables do. Additionally, FFCs are more adaptable, and improve the mitigation of electromagnetic interference.
The industry uses FFCs as the most popular cable connection solutions for many applications. As FFCs offer very high density along with a flexible structure, the industry uses them for many sophisticated applications, such as in laser printers, 3D printers, test equipment, and industrial displays. They are also applicable in membrane switches, medical equipment, household appliances, data systems, hard drives, and many more.
Various Types of Flex PCB Connectors
The industry uses various types of FPCs. Common types are:
Single-Layer FPC
The single-layer FPC has a single conducting layer. Depending on the application, these FPC may be made of plastic film or rust polymer. Single-layer FPCs are the cheapest connectors in the market.
Two-Layer FPC
The two-layer FPC has two conductive layers. In specific cases, the conductive layers may include driver ICs.
Multi-Layer FPC
As the name suggests, multi-layer FPCs have at least three conductive layers. Multi-layer FPC connectors are expensive and may include driver ICs in some of the conductive layers.
Important Parts of Flex PCB Connectors
Although one of the thinnest parts in the PCB industry, the construction of FPCs requires some important parts. Primarily, FPCs have three parts:
Body
Almost all FPC connectors have a plastic body. This is adequately sturdy for withstanding harsh conditions that the connector might face. The body provides the connections with the necessary mechanical stability.
Terminals
Terminals form the significant part providing the necessary electrical connections. Each contact has two functions—one to make contact with the circuit on the PCB, and the other to connect to the external circuit. For both functions, it is necessary for the terminals to be mechanically and electrically compatible.
Locking Arrangement
The locking arrangement mechanically locks the external circuit to the connector once it is firmly pushed in. The locking arrangement is strong enough to withstand repeated use. Typically, it is made of polyphenylene sulphide for providing the necessary stiffness.
Connecting Flex PCB Connectors
With almost all electronic equipment becoming smaller and thinner, it is necessary that the connectors that they use are not only simple to assemble, but also are space-saving.
Such electronic equipment, like cameras, tablets, computers, and smartphones typically use FPC connectors with a 0.2 mm pitch. Not only do these FPCs offer small pitch, but they are also of very small height.
Ear tabs on the connector housing of the FPC help in the alignment during cable insertion. The terminal casing is typically white, which makes it easier to locate and position the cable.
Some FPCs also provide Zero Insertion Force. They have terminal contact gaps that are larger than the cable thickness. The actuator opens and rotates to about 130 degrees, allowing for easy cable insertion. Once the cable is properly in place, the actuator can be rotated back and locked into position. Internally, the terminals move to make proper contact with the cable, before it is locked into place.
Features of Flex PCB Connectors
Manufacturers of FPCs offer several features with different types. Primarily, these are:
- Flex PCB connectors use flexible FPC and FFC cables
- Both ZIF or Zero Insertion Force and Non-ZIF or Non-Zero Insertion Force connectors are available
- It is possible to have top, bottom, and dual contact versions of FPCs
- Installing FPCs does not require any tools
- FPCs are very thin and lightweight
- FPCs are specially designed for low profiles
- 25-pitch series are popular in FPCs
Why Use Flex PCB Connectors
FPCs have brought about a revolution in the electronic industry. This is due to their compact size, low profile, and sturdy construction. The major benefit of these connectors is the high density of interconnectivity they can provide with their simple construction. Other benefits of FPCs are:
- Flexibility: This is a major advantage, especially when the connectors are used with flex PCBs. The use of flexible materials for making these connectors also make them more reliable. Being foldable and bendable, FPCs provide a secure connection between the FPC edge connector and the PCB header.
- Lightweight: FPCs are designed to be lightweight. Being small in dimension, the FPC connector saves a lot of space, especially in complicated and tightly fitting assemblies.
- Long Life: FPCs typically have a long service life. On a modest scale, they can survive at leat 200 thousand insertions.
- Reliability: Because they are made of materials that can bend and flex easily, FPCs can withstand higher levels of vibration as compared to what other types of connectors can.
- High Speed: FPC connectors are available for interconnecting high-speed and high-frequency circuits.
- SMD Compatibility: FPCs are compatible with SMD technology.
- Good Thermal Properties: The materials used for making FPCs are highly temperature resistant—they can withstand high temperatures.
- Corrosion Resistant: FPCs are made from materials that can not only resist corrosion, but is also water-resistant, resistant to moisture, and shock-resistant. This allows FPCs to be highly functional in hostile environments.
- Cost-Effective: The small size and high functionality of FPCs makes them very cost-effective.
Different Connector Styles for Flex PCB Connectors
Zero Insertion Force Types
These are IC socket type of connector that can be easily connected as they require very little insertion force. Although more expensive compared to standard connectors, ZIF connectors use an actuator that opens to receive the flex cable and then locks it into place.
Eminently suitable for applications subject to high vibrations, ZIF connectors reduce the stress and wear on contacts, thereby improving their working life.
Non-Zero Insertion Force Types
This type of connector makes use of frictional force to ensure a proper connection of the flex cable. However, this reduces the mating cycle, and is suitable for static applications. The non-ZIF connector is smaller and lighter than its ZIF connector counterpart, and also less expensive.
Conclusion
The flex PCB connector has been a boon to the electronic industry, allowing OEMs to manufacture devices with thinner and smaller form factors. Rush Flex PCB recommends using FPCs for all upcoming future electronic projects. The high quality of manufacturing that goes into manufacturing flex PCB connectors make them worth the investment.