All About the Flex PCB Assembly Process
Flex PCBs are printed circuit boards that have been manufactured using substrates that are naturally flexible. Manufacturers typically fabricate flex circuits using polyimide materials like Kapton and one or multiple layers of copper foil. Other popular flex materials include DuPoint and Panasonic. At Rush Flex PCB, we stock all types of flex substrate materials.
Typically, a flexible printed circuit board material will bend, but not snap like an FR4 board will. However, the copper foil on the flex board will likely crack if the bend creates a crease. It is easy to confuse a flex board with a very thin FR4 board, which may be semi-flexible. Although a thin FR4 board of less than 10 mil thickness can flex, it will eventually snap, as FR4 material is brittle.
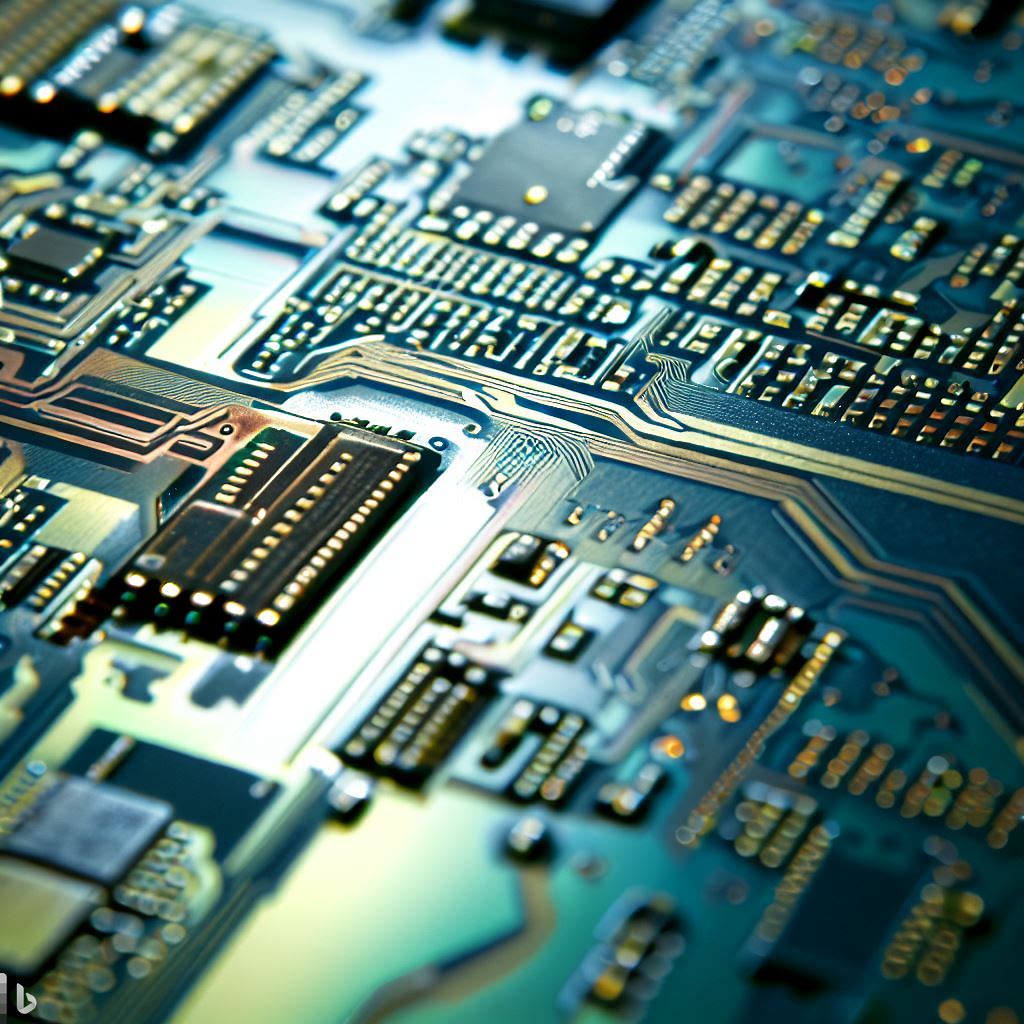
Rigid and Flex Boards Differences
There are several differences between rigid and flex boards:
Material
While rigid boards are typically made of glass-epoxy compounds like FR4, flexible circuits are made from Polyimide. This gives flexible circuits the ability to bend without breaking.
Coverlay
While rigid boards only have a solder mask for protection, flexible boards can have either a flexible mask or a coverlay. With a coverlay, the fabricator typically laser cuts the necessary openings. The coverlay has an adhesive layer of 1 to 2 mils thickness to allow it to adhere to the flex board surface.
Stiffeners
Manufacturers use stiffeners on flex boards to stiffen their non-flexing regions. The stiffeners can be either FR4, polyimide, aluminum, or steel. They either laminate the stiffener to the flex or attach it using a pressure sensitive adhesive. Rigid boards, as their name suggests, do not require stiffeners.
Permittivity
Rigid boards, being made from a variety of materials, can have a wide range of relative permittivity or dielectric constants. However, flex boards do not have a range, because they are made mostly of polyimide material with a dielectric constant of 3.4.
Types of Flex PCBs
Flex PCBs are classified into three types:
Flexible PCBs
These boards are fully flexible, but can have stiffeners for areas with ZIF sockets.
Flex PCBs with Stiffeners
When it is necessary to stiffen the flex board in certain areas, manufacturers add stiffeners. These are suitable for flex circuits that have components mounted only on one side.
Rigid-Flex PCBs
These are a combination of rigid and flex circuits. Manufacturers sandwich the flexible layers between the rigid ones, typically using no-flow prepreg. These are suitable for flex circuits with components on both sides.
Why Use Flex Circuits?
There are several advantages of using flex circuits:
Weight—Flex circuits are much lighter than FR4 boards. This is due to two factors. One, flex boards are typically thinner than FR4 boards are, and second, polyimide material, of which flex boards are made, is much lighter than the glass-epoxy material of FR4.
Thin—Flex circuits are much thinner than regular FR4 boards. For a typical 2-layer flex board, the thickness can range from 4 to 10 mils.
Flexible—As the name suggests, flex boards are meant to be able to bend without breaking. On the other hand, rigid boards will snap when bent, as they are brittle.
High Temperature—As compared to the glass-epoxy material of rigid FR4 boards, the polyimide material of flex boards can withstand much higher temperatures. In addition, the flex material is resistant to many acids, gases, and oils.
Flex PCB Assembly Process
Although both use the same surface mount technology for assembly, the process for assembly of a flex board is very different from that of a rigid FR4 board. This is due to the flexible nature of the flex board, which requires the use of a dedicated carrier board to support it and give it the necessary stiffness.
Baking
Most flex boards are relatively soft, and manufacturers usually do not vacuum pack them when dispatching the boards. Therefore, they can easily absorb moisture during transportation and storage, and require baking before assembly. Baking is necessary to slowly force the moisture out from the boards. If this is not done, the high temperature impact within the reflow oven will quickly vaporize the water vapor in the flex board, which will emerge forming defects like blisters and delamination.
Baking conditions generally require a temperature of 80-100 °C, for about 4 to 8 hours. If necessary to bake for shorter periods, the temperature may be raised to 125 °C. Prior to baking, a sample test is recommended to ascertain if the flex board can withstand the baking temperature. The manufacturer may also be consulted for suitable baking conditions.
Assembly Carrier Fixture
As stated earlier, flex boards require a carrier fixture to give them the necessary stiffness. To make the carrier fixture, it is necessary to manufacture a high-precision positioning template based on the drilling hole layer file of the flex board. It is essential that the diameter of the pin on the positioning template be the same as the diameter of the positioning hole on the carrier board, and matches with the hole diameter on the flex board.
The flex board may not be the same thickness throughout. Some part of the board may be thicker than the others by design, while other areas may have stiffeners making them thicker. The carrier board must follow the thickness difference to allow the flex board to remain flat during the printing and placement process. The material of the carrier board will have to be light and thin, of high strength, capable of low heat absorption, high heat dissipation. It must also not warp and deform after several thermal shocks. Manufacturers typically use special high-temperature materials like magnetized steel, silica-gel plate, aluminum, and synthetic stone for making the assembly carrier fixtures.
Positioning the Flex Board
Before starting the surface mount process, it is necessary to accurately fix the flex board to the carrier board. There can be two types of carrier boards, one with positioning pins, and others without. Carrier boards without positioning pins need a positioning template with positioning pins.
The carrier board must be placed on the template to expose the positioning pins through the holes on the carrier board. The flex board must now be placed aligning it on the positioning pins. After fixing the exposed positioning pins with tape, the carrier board may now be separated from the positioning template. The carrier board is now ready for further processing—printing, mounting, and soldering.
Solder Paste Printing
Most of the solder paste printing process for flex boards is the same as that for rigid boards. The solder paste composition can also remain the same, easy to print and release. It should adhere firmly to the surface of the flex board. The stencil design should allow easy release, with not blocking, no leakage or collapse after the stencil has been lifted after printing.
The squeegee or scraper for moving the solder paste on the flex board should not be made of metal. As the flex board is mounted on the carrier board, its plane is not perfectly flat, and the thickness and hardness may be inconsistent. It is recommended to use a polyurethane scraper with a hardness of 80-90 degree. This allows the scraper to adjust to the tiny gaps between the flex board and the carrier board surfaces. It may be necessary to experiment with the degree of the scraper for the best printing effect.
Surface Mount Component Assembly
The process for mounting SMCs on flex boards is not much different from that for rigid boards. However, due to partial air gaps between the flex board and the carrier board, it may be necessary to adjust the suction nozzle drop height and the blowing pressure. It may also be necessary to reduce the moving speed of the nozzle, and this may reduce the yield of the assembly line for flex boards.
Reflow Soldering Process
Unlike the reflow process for soldering rigid boards, the soldering process for flex boards requires infrared reflow ovens to use forced hot air convection. This is necessary to maintain a uniform temperature over the entire flex board. Typically, four corners of the flex board are fixed to the carrier with tape, and the center of the board can rise or fall to deform under hot air. Therefore, it may be necessary to adust the velocity of the hot air appropriately.
Thermal Profile Setting
Different heat absorption properties of the components on the flex board and the carrier board material may cause the temperature to rise at different rates during the reflow soldering process. This requires a carefull setting of the temperature curve in the reflow oven for improving the quality of soldering.
Inspection and Testing
After soldering, the assembled flex board can be visually inspected under a lighted magnifying glass for solder defects, resident glue, solder beads, no solders, shorts, and other problems.
As the surface of flex PCBs is not smooth, it is difficult to use Automated Optical Inspection methods. Also the soft nature of the boards requires special test fixtures for ICT or In-circuit testing, and FCT or function circuit testing.
Separating
Most flex boards are connected for ease of assembly, and it is necessary to separate them before testing. Although it is possible to use manual tools for separating the flex boards, the scrap rate is likely to be high. It is recommended to use stamping and splitting dies for separating the flex boards, as they improve the efficiency significantly. They also make the edges of the flex boards clean and well-cut, while protecting the inner surfaces from undue stress.
Conclusion
Rush Flex PCB recommends using strict production process management for assembling flex boards. Operators must implement all requirements of the standard operating procedures. In-process quality controllers and engineers must inspect appropriately, and analyze the causes for failures and abnormal assembly conditions. They must also take necessary action for controlling the defect rates of the production line within the specified PPM.